Design Improvements (Sheet Metal)– Hexagonal Heater Casing
We caught up with Graham Gee, St Ann’s Sheet Metals’ Project Development Engineer, on a recent visit, and he showed us one of his latest Design Improvements he has been involved in. The customer is extremely happy with this re-design, and so are we, as it is now better, smarter and easier making it far more cost-effective to manufacture. It is one of our many design improvements that we offer as standard. Why not get your sheet metal project redesigned by us?
WHAT INITIATED THE PROJECT?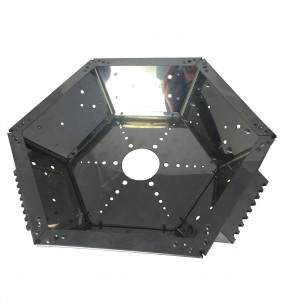
“On seeing the item that the customer brought to us to replicate, I instantly saw room for improvement on the current manufacturing method. By redesigning the unit and altering the method of fabrication we would be able to reduce the cost and speed up both the manufacturing time and the customer’s assembly time as well.”
HOW WOULD THIS BE ACHIEVED?
“Although the unit was suited to the job it was required to do, it lacked the modern techniques of manufacture. Instead of building the unit in eight individual pieces we were able to reduce the component parts to just two. This in itself removed any unnecessary assembly fixings by more than half.”
WHAT TECHNICAL UNCERTAINTIES/PROBLEMS DID YOU ENCOUNTER AND HOW DID YOU OVERCOME THEM?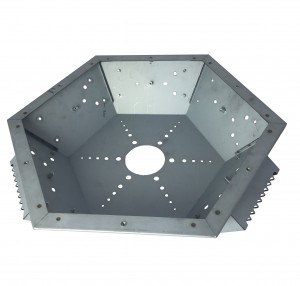
“The main issue came from reducing the number of operations required to produce the unit in its existing form, to producing in a way that would be more cost-effective. As we were able to laser cut intricate internal cut-outs it allowed us to eliminate 60 individual fixing points by bending the casing in one piece, which also reduced the total amount of bends from 42 down to just 24. Because this design made the unit more rigid I was also able to reduce the thickness of material which helped save cost. In order to hold the unit together at the joins, I manipulated existing resistance weld tooling so that the unit could be spot-welded at the join, hiding any weld burn marks.”
WHAT TRIALS AND EXPERIMENTS DID YOU UNDERTAKE?
“We proceeded to act on our design, with the customer requesting us to build samples, which we were happy to do. The initial prototypes were originally designed by myself and drafted in our 3D CAD software. This helped to highlight any potential faults before any prototypes were made. The finished prototypes were very successful, achieving everything we had set out to do, and the customer was extremely happy with the cost savings the new design offered.”
WHAT IS THE OVERALL RESULT OF THE PROJECT?
“At present the project is due for trial in the next couple of weeks. Not only have we given the customer the unit they were looking for, but we have also saved cost in manufacturing and the customer’s assembly.”
IS THE PROJECT ONGOING & WILL YOU CONTINUE TO DEVELOP IT IN THE FUTURE?
“The project is still ongoing, and the next step is to offer the heater casing as a powder coated unit as well as the current Stainless Steel material. As with this and many other projects undertaken we are constantly looking for ways to improve on our processes. As new technology & techniques become available we will look to use this in our production methods and hopefully continue to offer cost savings to our customers”