Aluminium Welding - A Bit About Aluminium
Aluminium Welding is a highly sort after skill and you might be wondering why that is. Well, the high strength, lightweight and none corrosive properties of aluminium makes it a valuable resource. Especially when an engineer's design depends on the items weight and longevity. On top of that the finish on aluminium makes it an aesthetically pleasing material to work with.
Click here for more information about the benefits aluminium.
Because of this, aluminium is a highly sought after material. One that a lot of engineers like to include in their designs when weight, strength or longevity vital to the end product.
The big issue though is due to the heat conductivity and relative softness of the aluminium. These factors along with it’s tendency to gain impurities whilst in its molten state that makes aluminium welding extremely difficult. At least for inexperienced welders.
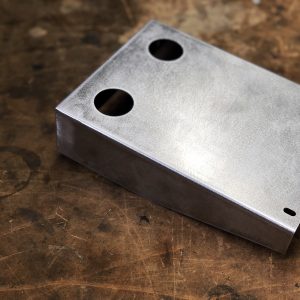
What Makes Aluminium Welding So Difficult?
The melting point of pure aluminium alone is 650℃. The fact that the melting temperature for the metal itself is so low wouldn’t be an issue in and of itself. The issue is around the oxide that naturally forms on the surface of the material. The melting point for the oxide on the surface is a significantly higher 2,037℃.
This makes it incredibly important for the welder to monitor the temperature as they weld. This is because the welder needs to ensure that the flame is hot enough to burn through the tough oxide layer, whilst being careful not to burn through the aluminium itself.
This coupled with aluminium’s high heat conductivity mean that aluminium welds not only need to be done quickly but also accurately and with a high level of attention to detail. A level only gained through experience.
What Do We Need To Do To Weld Aluminium?
If aluminium is not welded quickly enough and is left at a high temperature then it can lead to weaker welds. This is due to the aluminium absorbing hydrogen from the air at higher temperatures. As the aluminium cools the hydrogen then begins to separate back out of the metal, leaving bubbles in the material. The end result is a weaker, porous weld.
The only way to resolve this and weld quickly is to weld at a higher temperature, which has stated above runs the risk of burning through the material and ruining the integrity of the material.
Striking the balance is what makes our welders so valuable to our business and our customers.
What Can We Offer?
The skill and experience of our welders means that we’re able to offer up a range of options when it comes to welding. There’s the standard weld options of TIG and MIG welding (more about them in later posts). But we can also use filler materials to cover aluminium’s naturals weaknesses. If filler material is used, our expert welders will choose a material based upon the proper composition needed to get the job done.
To find out more, why not use the get a quote button above to let us know what your looking for?